Conheça a metodologia lean e como aplicar seus princípios!
Descubra como a Lean pode transformar os processos da sua empresa, com ênfase em seus princípios e desperdícios. Aprenda a implementar e otimizar seu fluxo.

O Lean, também conhecido como "Produção Enxuta", é uma metodologia de gestão que surgiu no sistema de produção da Toyota no Japão. Seu objetivo é maximizar o valor para o cliente, eliminando qualquer atividade que não agregue valor ao produto final.
Em outras palavras, o Lean busca otimizar processos, reduzir desperdícios e aumentar a eficiência, entregando produtos e serviços de alta qualidade com o mínimo de recursos.
Desta forma, a implementação da metodologia ajuda empresas de diferentes portes e segmentos a reduzir custos, melhorar a qualidade, aumentar a produtividade e, consequentemente, se tornarem mais competitivas no mercado.
Além disso, o Lean também é importante porque promove uma cultura de melhoria contínua, incentivando os colaboradores a identificar e eliminar problemas, o que resulta em um ambiente de trabalho mais eficiente, dinâmico e motivador. Conheça mais sobre os princípios, benefícios e dicas de como aplicar!
Quais são os 5 princípios do Lean?
O Lean é baseado em cinco princípios que são o ponto de partida para colocar a metodologia em prática. São eles: identificar o valor, mapear o fluxo de valor, criar fluxo contínuo, estabelecer a produção puxada e buscar a perfeição. Vamos conhecer melhor cada um deles!
1. Valor
Esse é princípio guia as decisões de produção e os processos da empresa ao direcionar todas as ações para atender às necessidades e expectativas do cliente. O "Valor", no contexto do Lean, é definido pelo cliente e refere-se a tudo aquilo que ele está disposto a pagar por um produto ou serviço.
A empresa que consegue entender o que o seu cliente considera valioso também consegue criar as condições perfeitas para adaptar seus produtos e serviços, otimizar a cadeia de suprimentos e personalizar a experiência de consumo.
A identificação do valor permite ainda que a empresa concentre seus recursos nas atividades que geram maior impacto nos resultados, aumentando a eficiência e a competitividade, eliminando desperdícios e otimizando processos.
2. Fluxo de valor
Depois de identificar o valor, é necessário mapear todas as etapas do processo, desde a aquisição de matéria-prima até a entrega ao cliente. Isso permite visualizar o fluxo e identificar as atividades que não agregam valor, ou seja, os desperdícios.
Mapear o fluxo de valor significa visualizar detalhadamente todas as etapas envolvidas na criação de um produto ou serviço, desde a aquisição de matérias-primas até a entrega ao cliente. Essa visualização permite identificar os desperdícios, como esperas, retrabalhos e excesso de estoque.
Com a identificação desses desperdícios, fica mais fácil otimizar os processos, eliminando atividades que não agregam valor e tornando o processo mais eficiente.
Somado a isso, o mapa do fluxo de valor serve como uma ferramenta de comunicação, já que permite que todos os envolvidos no processo consigam visualizar como suas atividades se encaixam no todo.
Ferramentas como o Value Stream Map (VSM) e diagramas de processo podem ser utilizadas para criar esse mapeamento.
3. Fluxo contínuo
O terceiro princípio, do fluxo contínuo, está focado em eliminar interrupções e atrasos ao longo do processo produtivo, buscando atingir um fluxo constante de produção.
A ideia é que cada etapa do processo alimente a próxima sem interrupções, como uma linha de montagem perfeita. Para isso, as empresas devem focar em otimizar o layout da fábrica, reduzindo ao máximo os deslocamentos de materiais e pessoas.
Ainda, a redução dos tempos de setup entre as diferentes etapas do processo, a identificação e a eliminação de gargalos desempenham um papel relevante na busca por um fluxo contínuo. Para garantir bons resultados neste processo, as empresas podem adotar algumas estratégias como:
implementação de células de produção, que agrupam as máquinas e os operadores necessários para a produção de um determinado produto ou família de produtos, prática que ajuda a reduzir os deslocamentos e facilita a comunicação entre os colaboradores;
uso de sistemas de produção puxada evita a produção em excesso e garante que os produtos sejam produzidos apenas quando são necessários;
padronização dos processos, para que que todas as atividades sejam realizadas da mesma forma, reduzindo a variabilidade e os erros.
A implementação do fluxo contínuo traz uma série de benefícios, como a redução dos tempos de ciclo, a diminuição dos estoques, a melhoria da qualidade dos produtos e o aumento da satisfação dos clientes.
4. Sistema de pull (puxe)
A produção puxada consiste em produzir apenas o necessário e no momento em que é necessário. Esse princípio é voltado para a lógica: a demanda do cliente "puxa" a produção, prática que ajuda a evitar o acúmulo de estoques e a produção de itens que não serão vendidos.
Dessa forma, em vez de produzir com base em previsões, a produção é acionada apenas quando há um pedido do cliente. Imagine uma fábrica de bicicletas: no sistema tradicional, bicicletas são produzidas em massa e armazenadas. No sistema pull, a produção só começa quando uma bicicleta é vendida.
Essa mudança reduz custos de armazenamento e aumenta a flexibilidade, permitindo que as empresas se adaptem rapidamente às mudanças nas demandas dos clientes. Exemplos práticos incluem a indústria automobilística, que configura veículos sob demanda, e o e-commerce, que personaliza produtos após a confirmação do pedido.
5. Perfeição
Por fim, o quinto princípio consiste na busca pela perfeição e representa um compromisso constante com a melhoria. Essa busca envolve a identificação e a eliminação sistemática de desperdícios, como retrabalho, espera e transporte desnecessário.
Combine essas práticas com a implementação de novas ideias e tecnologias que ajudam a otimizar os processos e aumentar a eficiência. A melhoria contínua é impulsionada por feedbacks constantes de clientes, colaboradores e dados de desempenho.
Por meio da análise desses dados, as empresas podem identificar oportunidades de melhoria e implementar ajustes nos processos. Essa cultura de melhoria constante não apenas aumenta a qualidade dos produtos e serviços, mas também mantém as empresas competitivas.
Quais são os 7 desperdícios do Lean?
A metodologia, baseada nos cinco princípios que apresentamos, tem como propósito comum eliminar sete desperdícios: tempo de espera, defeito, transporte, movimentação, estoque, superprodução e superprocessamento. Continue a leitura e conheça!
1. Tempo de espera
O primeiro desperdício a ser eliminado é o tempo de espera, termo usado para se referir a qualquer interrupção no fluxo de trabalho que causa atrasos na produção. Seja um equipamento parado por falta de manutenção, um operador aguardando por materiais ou uma informação que demora a chegar, o tempo de espera impacta diretamente a eficiência e a produtividade.
Para reduzir o tempo de espera e otimizar o tempo de ciclo, é necessário analisar o fluxo de trabalho de forma detalhada, identificando os gargalos e as causas das interrupções. Um planejamento estratégico bem elaborado, que considere a capacidade de produção, a demanda e os recursos disponíveis, pode ajudar nesse sentido.
Além disso, a organização do layout da fábrica, a padronização dos processos e a implementação de sistemas de produção puxada podem contribuir consideravelmente para a redução dos tempos de espera e a otimização do fluxo de trabalho.
2. Defeito
Defeitos em produtos ou serviços representam um dos maiores desperdícios em qualquer processo produtivo. Quando um produto apresenta defeito, ele precisa ser retrabalhado, reprovado ou até mesmo descartado, gerando custos adicionais e atrasos na entrega.
Os defeitos também podem comprometer a reputação da empresa e a satisfação do cliente. A ocorrência de defeitos, muitas vezes, está relacionada a falhas nos processos, falta de treinamento dos colaboradores ou variações na qualidade dos materiais.
Nesse cenário, a automação de processos, quando aplicada de forma estratégica, pode contribuir para a redução do problema, já que diminui a possibilidade de ocorrência de erros humanos e garante maior consistência na produção.
A implementação de sistemas de controle de qualidade e a utilização de ferramentas estatísticas também são interessantes para identificar as causas dos defeitos e implementar ações corretivas.
3. Transporte
O transporte, como um dos sete desperdícios do Lean, refere-se a qualquer movimentação de materiais que não agrega valor ao produto final. Essa movimentação desnecessária gera custos adicionais, aumenta o risco de danos e atrasos na entrega.
Para otimizar a logística e reduzir esse desperdício, a empresa pode realizar uma análise SWOT do processo de transporte, identificando os pontos fortes, fraquezas, oportunidades e ameaças.
A partir dessa análise é possível implementar melhorias, como a otimização do layout da planta, a redução das distâncias percorridas pelos materiais e a adoção de soluções de transporte mais eficientes, como o uso de carrinhos de transporte, esteiras rolantes ou sistemas automatizados.
4. Movimentação
Movimentos físicos desnecessários de pessoas, materiais ou equipamentos dentro de um processo produtivo geram perda de tempo, aumentam o risco de acidentes e podem causar fadiga nos colaboradores.
Para reduzir a movimentação, é preciso reorganizar o espaço de trabalho de forma a minimizar as distâncias percorridas e otimizar o fluxo de materiais. A implementação de células de trabalho, em que todas as ferramentas e materiais necessários estão à mão do operador, é uma prática comum para reduzir a movimentação.
A prática pode ser combinada com a automatização de tarefas repetitivas, como o transporte de materiais entre diferentes etapas do processo, eliminando a necessidade de movimentação manual.
5. Estoque
O Just-in-Time (JIT) é uma filosofia de gestão que visa eliminar desperdícios e otimizar a produção. Produzindo apenas o necessário e no momento exato, o JIT reduz os níveis de estoque, liberando capital e espaço físico.
A sincronização entre as etapas do processo produtivo, característica do JIT, melhora o fluxo de produção, reduzindo os tempos de espera e aumentando a eficiência. A otimização do uso de recursos, como materiais e mão de obra, é outra consequência do JIT, pois evita a produção de itens que não serão utilizados imediatamente e direciona os esforços para atender à demanda real do cliente.
6. Superprodução
Para adotar uma produção baseada na demanda real do cliente e evitar a superprodução, empresas podem implementar o sistema puxado. Lembra que já falamos sobre ele? Nesse sistema, a produção é iniciada apenas quando há um pedido do cliente, eliminando a necessidade de grandes estoques e reduzindo o risco de produzir itens que não serão vendidos.
O sistema puxado funciona como uma cadeia, em que cada etapa da produção é acionada pela etapa anterior, garantindo que a produção esteja sempre alinhada com a demanda. Para implementar esse sistema, as empresas podem utilizar ferramentas como o Takt Time, que define o ritmo de produção necessário para atender à demanda do cliente.
7. Superprocessamento
Simplificar processos no Lean consiste em analisar cada etapa da produção, identificando e eliminando aquelas que não agregam valor ao produto final. Reduzindo o número de etapas, diminui-se a possibilidade de erros e retrabalho, otimizando o tempo de produção e liberando recursos.
A simplificação dos processos permite, ainda, uma melhor visualização do fluxo de trabalho, facilitando a identificação de gargalos e a implementação de melhorias. A eficiência dos recursos também é aprimorada, pois ao eliminar etapas desnecessárias, menos recursos são utilizados, como mão de obra, energia e materiais.
Para alcançar a simplificação dos processos, é fundamental envolver os colaboradores na análise e proposição de melhorias, utilizando ferramentas como o mapeamento do fluxo de valor e o 5S para organizar o ambiente de trabalho e padronizar as atividades.
Benefícios da metodologia Lean para as empresas
A metodologia Lean, focada na eliminação de desperdícios e na otimização de processos, traz uma série de benefícios para as empresas que a implementam. Entre os principais, destacamos:
redução de custos associados à diminuição de estoques, a redução de defeitos e a otimização do uso de recursos;
aumento da eficiência e produtividade, atrelada à simplificação dos processos e otimização do fluxo de trabalho resultam em um aumento da eficiência e da produtividade;
melhora da qualidade dos produtos e serviços que se reflete na maior satisfação do cliente e em uma melhor reputação da marca.
A Toyota, pioneira no setor automotivo, é amplamente reconhecida por sua implementação bem-sucedida do Lean Manufacturing. O Sistema de Produção Toyota (TPS), fundamentado nos princípios Lean, foi crucial para o sucesso da empresa, otimizando processos, reduzindo desperdícios e aumentando a eficiência.
A John Deere, líder na fabricação de equipamentos agrícolas, também abraçou a filosofia Lean, implementando-a em suas unidades produtivas. Essa adoção resultou em uma redução expressiva dos custos de produção e em uma melhoria significativa na qualidade de seus produtos, consolidando ainda mais sua posição no mercado.
Como implementar a metodologia Lean na sua empresa?
Se você tem interesse em implementar a metodologia na sua empresa, montamos um guia com um passo a passo simples que pode auxiliar nessa jornada. Confira!
Faça o mapeamento do fluxo de valor, definindo o processo a ser analisado, desde a perspectiva do cliente até a entrega final. Crie um mapa visual do processo, identificando todas as etapas, atividades e fluxos de materiais e informações.
Analise cada etapa, identificando atividades que não agregam valor e desperdícios.
Identifique os sete desperdícios no contexto do mapeamento realizado. Priorize aqueles que mais impactam o processo e implemente ações para eliminar ou reduzir cada desperdício identificado.
Crie um fluxo contínuo — organize as estações de trabalho para garantir um fluxo contínuo de produção, minimize o tempo de setup das máquinas e equipamentos, identifique e elimine os gargalos que impedem o fluxo contínuo.
Sistema puxado — produza apenas o necessário e no momento certo, e implemente o sistema Kanban para controlar o fluxo de produção e evitar a superprodução.
Melhoria contínua — incentive os colaboradores a buscarem continuamente melhorias em seus processos e implemente metodologias como a 5S para organizar o ambiente de trabalho e facilitar a identificação de problemas.
Implemente sistemas de medição — defina indicadores-chave de desempenho (KPIs) para acompanhar o progresso da implementação do Lean. Use os dados coletados para ajudar as ações e melhorar o processo de tomada de decisão.
Onde a metodologia Lean pode ser aplicada?
A metodologia Lean, originalmente desenvolvida para a indústria manufatureira, tem demonstrado sua versatilidade e pode ser aplicada em diversos setores, desde a produção em massa até a prestação de serviços.
Setores como o automotivo, eletrônico, de saúde, bancos, hotelaria, tecnologia da informação, governo, educação e construção civil têm se beneficiado da aplicação do Lean, otimizando processos, reduzindo desperdícios e aumentando a eficiência.
A chave para o sucesso está em adaptar os princípios do Lean à realidade específica de cada setor, buscando sempre a eliminação de atividades que não agregam valor e a melhoria contínua dos processos.
Ferramentas Lean para a melhoria contínua
O Lean oferece um arsenal de ferramentas. Entre as mais populares, destacam-se o Kaizen, o Kanban e o 5S. O Kaizen, filosofia de melhoria contínua, incentiva todos os colaboradores a propor e implementar pequenas mudanças para otimizar processos e eliminar desperdícios. Um exemplo prático é um funcionário sugerir uma nova forma de organizar ferramentas, reduzindo o tempo de busca e aumentando a produtividade.
O Kanban, por sua vez, utiliza um sistema visual para gerenciar o fluxo de trabalho, permitindo identificar gargalos e otimizar a produção. Em uma fábrica, por exemplo, o Kanban pode ser utilizado para controlar o número de peças em cada etapa do processo, evitando a superprodução e a falta de material.
Já o 5S foca na organização do ambiente de trabalho por meio de cinco passos: senso de organização, senso de ordem, senso de limpeza, senso de padronização e senso de disciplina. Um exemplo claro é a organização de um estoque, com a identificação de cada item e a definição de um local específico para cada um, facilitando a localização e evitando a perda de tempo na busca por materiais.
A combinação dessas ferramentas, quando aplicada de forma sistemática, permite que as empresas alcancem níveis mais altos de eficiência em diferentes níveis de operação.
Qual a diferença entre metodologia Lean e Six Sigma?
O Lean e o Six Sigma são duas metodologias que visam a melhoria contínua dos processos, mas com focos distintos. O Lean busca a eficiência operacional por meio da identificação e eliminação de desperdícios em todos os processos, otimizando o fluxo de trabalho e reduzindo o tempo de produção.
É diferente do Six Sigma, que tem como objetivo principal a redução da variação dos processos e a melhoria da qualidade, utilizando ferramentas estatísticas para identificar e eliminar as causas dos defeitos, garantindo que os produtos e serviços atendam aos requisitos dos clientes com um nível de qualidade consistente.
Ou seja, enquanto o Lean se concentra em "fazer mais com menos", o Six Sigma busca a perfeição operacional, reduzindo a taxa de defeitos a níveis quase zero.
Como o Lean pode auxiliar na gestão de documentos?
A metodologia Lean pode contribuir eliminando etapas ineficientes, como a busca por documentos perdidos ou a redigitação de informações. A Lean agiliza o fluxo de trabalho, reduzindo o tempo e os custos envolvidos.
Ainda, a padronização dos processos e o uso de ferramentas visuais, como o Kanban, garantem que os documentos sejam processados de forma eficiente e com menor margem de erro.
Essa otimização se alinha perfeitamente com plataformas como a DocuSign, que automatizam a assinatura e gestão de contratos, eliminando a necessidade de imprimir, enviar e receber documentos fisicamente. Integrando a metodologia Lean com ferramentas digitais, as empresas podem alcançar um nível superior de produtividade, reduzindo custos e agregando valor aos seus negócios.
Como você viu, a metodologia Lean não se limita apenas à otimização de processos. Ela também promove uma mudança cultural nas organizações, incentivando o trabalho em equipe, a busca constante por melhorias e o envolvimento de todos os colaboradores.
Sua empresa busca metodologias, como o Lean, que podem contribuir para melhorar o desempenho organizacional? O que você acha de conhecer a Docusign? Entre em contato com a nossa equipe de vendas, solicite informações e comece a usar a tecnologia a favor da sua operação!
Diretora de marketing com ampla experiência na liderança da área de Marketing e comunicação. Forte orientação para resultados por meio de pensamento estruturado e ampla visão de negócio. Com grande experiência em corporate marketing e geração de demanda - Coordenando PR, Website, blog, social media, campanhas de marketing inbound e outband e eventos de todos os tamanhos, além do gerenciamento de equipe. Sólida experiência em entender as prioridades dos negócios e implementação de uma comunicação e de uma estratégia de marketing eficazes e voltada para resultados.
Publicações relacionadas
- Soluções para equipesPublicado em 12 de dez. de 2024
- Soluções para equipesPublicado em 11 de dez. de 2024
Balanced Scorecard (BSC): tudo o que você precisa saber
- Soluções para equipesPublicado em 9 de dez. de 2024
Ferramentas da qualidade: guia para otimizar processos empresariais
O que é a matriz GUT e como aplicá-la? Saiba agora!

Balanced Scorecard (BSC): tudo o que você precisa saber

Ferramentas da qualidade: guia para otimizar processos empresariais
Confira as novidades do Docusign IAM ou comece a usar o eSignature grátis
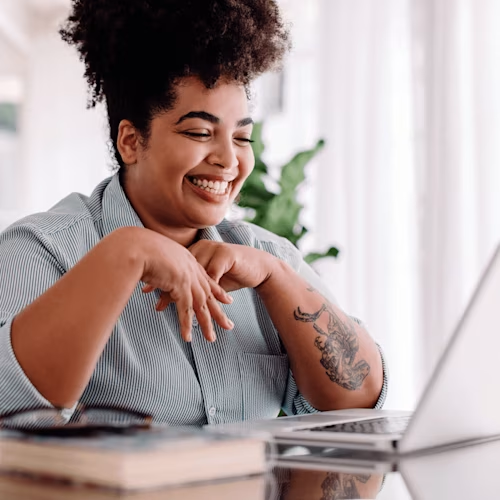