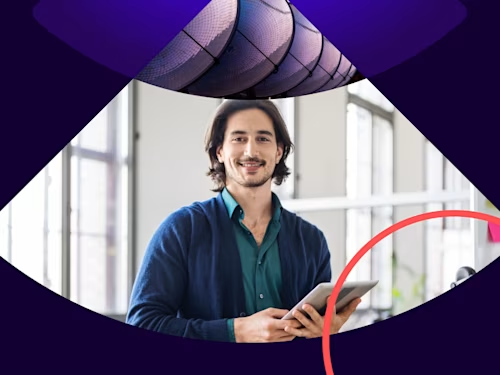
Industry spotlight: Bio-pharma company tackles a complex compliance conundrum with help from DocuSign
Our industry spotlight series shines a light on how companies solve unique challenges with help from DocuSign’s solution engineers. Here, Sanghun Woo shares how a pharmaceutical company bolsters productivity while maintaining compliance.
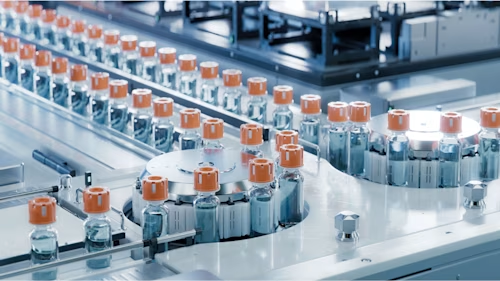
Our industry spotlight series shines a light on how companies solve unique challenges with help from DocuSign’s solution engineers. Here, Sanghun Woo shares how a pharmaceutical company bolsters productivity while maintaining compliance.
The pharmaceutical industry is heavily regulated. And for good reason. We all need the assurance that our medicines are safe, fit for use, and meet strict quality controls. Yet for the companies making these medicines, all that compliance and red tape can be incredibly time-consuming.
It’s why one of DocuSign’s bio-pharma customers recently approached us. They wanted a more streamlined, efficient way to handle the complexities of the global Good x Practice (GxP) rules.
One of the most well-known regulations in the pharmaceutical industry, GxP exists to protect public health by ensuring that medical products are reliable and effective. The “x” stands for the field the guidelines apply to. So, for example, GMP stands for Good Manufacturing Practice; GLP stands for Good Laboratory Practice; GCP stands for Good Clinical Practice; and so on.
Breaking down the 21 CFR Part 11
In the bio-pharma industry, a widely accepted foundation for complying with the GxP regulations is the 21 CFR Part 11 compliance (yes, that’s a mouthful. And, in case you’re wondering, CFR stands for Code of Federal Regulations). Essentially, it’s a set of rules defined by the United States Food and Drug Administration (FDA) around electronic records and signatures.
When it comes to electronic signatures, 21 CFR Part 11 compliance specifies that all changes, operations, inspection reports and so on relating to the manufacture of a new drug must not only be signed, but that information like timestamps, signer details, and signing reasons with signing-level login requirements are also captured. DocuSign eSignature can handle all this, not a problem, with our specific module for 21 CFR Part 11.
It does become a problem, though, when you have a separate eRecord system. If this system is not integrated with DocuSign, then users have to manually move the hundreds of forms that are signed for quality assurance (QA), inspection, training, and more — with documents flying back and forth between DocuSign and their eRecord system. It takes up a lot of time and manual effort.
This was the case for our bio-pharma company. Like many others in the life sciences industry, they use Veeva Vault as their eRecord system, and they wanted our help in integrating DocuSign’s 21CFR part 11 module with it. So we rolled up our sleeves and set to work.
A seamless integration
In partnership with Veeva Vault, we built a deep integration with the DocuSign 21CFR Part 11 module — leveraging the rich capabilities of the DocuSign API to ensure a seamless, scalable solution.
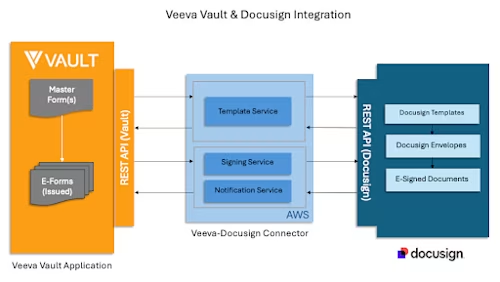
Veeva Vault and Docusign Integration Diagram 1
The integration covers four major steps enabling DocuSign signing features within Veeva Vault.
Step 1. Create and update a DocuSign template from Veeva Vault
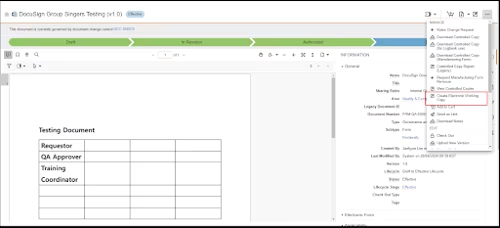
Veeva Vault and Docusign Integration Diagram 2
In Veeva Vault, the QC users can create a new DocuSign template and update it by referring to the master template in Veeva Vault using the CreateTemplate API.
Step 2. Initiate the signing process from Veeva Vault using Sender view
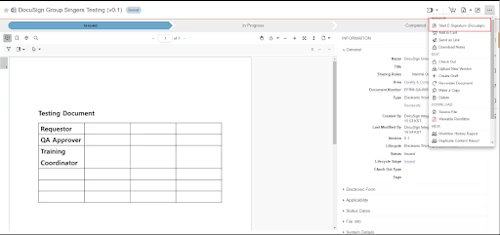
Veeva Vault and Docusign Integration Diagram 3
Once the DocuSign template is ready, the user can initiate the signing process from Veeva Vault. An envelope will be created referring to the template, and a sender view API call will be performed.
Create an envelope referring to the template API
Step 3. Manage envelope information in Veeva Vault
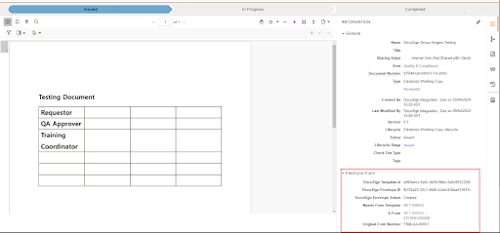
Veeva Vault and Docusign Integration Diagram 4
The user who initiates the signing process can see the status and envelope information details. DocuSign Connect was used with Webhook listeners for real-time updates.
Step 4. Archive signed copy, certificate of completion, and form data unlocking the next process and data analysis
Once the signing is completed, the signed copy and certificate of completion are archived automatically. The form data is archived in CSV format, and the customer plans to use this data for analysis purposes in the future.
A simpler, more streamlined system
Now, the bio-pharma’s quality control (QC) and quality assurance (QA) teams can get forms signed a lot faster and more easily than before.
The QC team can manage DocuSign templates from within Veeva Vault, and QA users can initiate and send signing requests from there, too — leveraging the template set up by the QC team. Further, they can see the signing status and archived signed copy in Veeva.
It means that users no longer need to switch applications. Instead, the whole signing process can be efficiently managed from the Veeva Vault — saving a lot of time and costs. Plus, because the new system expedites the entire GxP process, it lays the foundation for more revenue generation by the company. And all with the reassurance that they are ticking all the right regulatory boxes when getting new medicines ready for market.
Got a problem you need solving? As the above example shows, DocuSign’s solution engineers love a good challenge. If you’ve got a specific business problem that needs solving, get in touch to see how they can help you.
Related posts
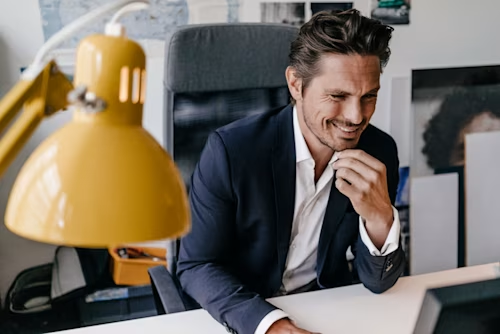
How to Simplify Contract Renewals
Discover what's new with Docusign IAM or start with eSignature for free
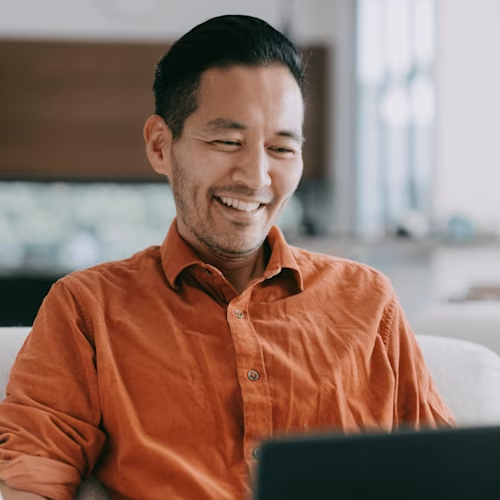